
How ENVE Makes Their Wheels and Frames - ENVE Factory Tour
We see ENVE Composites as one of the top carbon wheel brands on the market today. We kind of mean that literally; them being just 45 minutes north of us in Ogden, Utah means we could see them if we squint really, really hard. When it comes to manufacturing, however, they might as well be tops in the bicycle industry as they are one of the few to do all of their production in-house.
We had the opportunity as part of ENVE’s open house to receive a full tour of the ENVE facility to see just about everything they make. While we can’t share everything we were able to see, we’re here to share the good stuff that makes ENVE such a standup company in cycling.The tour more or less started in a machine shop. This machine shop is the basis to ENVE's carbon wheels. Knowing little about how carbon is made, I was surprised to see as big an areas as I did. This space seemed large enough to be its own factory, and they do output like one too; blocks of aluminum are cut by a cutter, after which they go into a CNC machine to be shaped and cut even more. Here’s they make hundreds of tools a day, and 48 alone for the ENVE Foundation 45 rim.

Historically, carbon rims have been made using bladders that could form to make hooked rims. Of course, those bladders need to be popped to be removed, meaning they could only be used once and sometimes led to less-perfect rim construction and tolerances. These CNC’d pieces of aluminum are how they make hookless carbon rims with more precise tolerances and stronger overall.
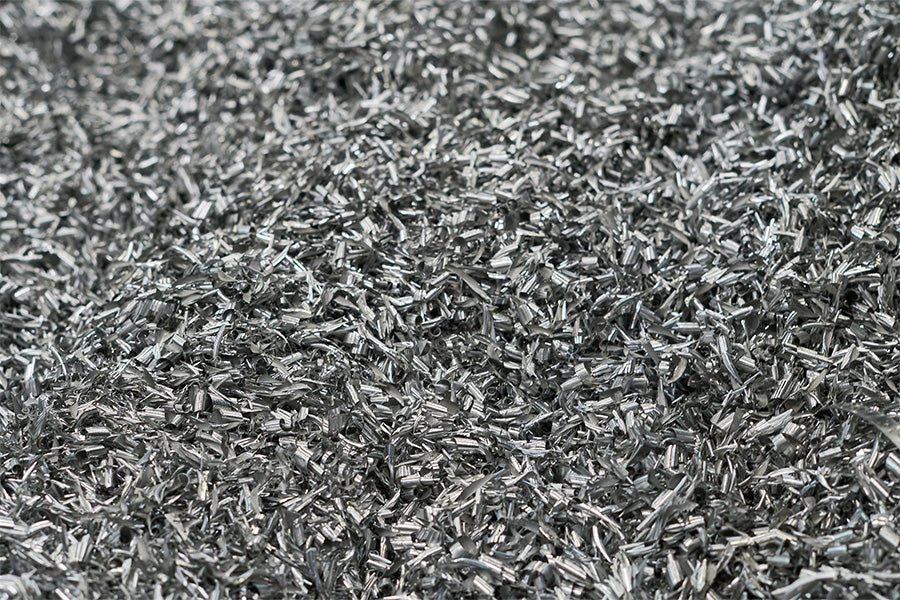
There’s so much metalwork going on that there are containers full of aluminum shavings! ENVE sources their carbon from Mitsubishi. Upon arrival, these carbon sheets are stored in a walk-in freezer placed just before the carbon-cutting room. This cutting room takes carbon and cuts them with templates to build. They only use unidirectional carbon fiber, which they say leads to stronger, more reliable wheels.
Not pictured are the machines that the carbon is fed into to form the rims, but is an impressive setup. While ENVE still has to use bladder molding to build some of their rims, most of their rims use those CNC’d aluminum molds. ENVE typically makes as many as 500 to 600 rims a day, and as many as 1000 rims per day.
One thing to note here is that most ENVE frames received molded spoke holes where the spoke interfaces with the rim. While more costly, molded spoke holes mean more continuous carbon fiber that leads to a stronger rim. The sanding machine still has holes to drill, largely for the outer wall that makes it easier to build a rim, but this area doesn’t experience nearly the same loads.
Carbon placed in clamshell molds go to an oven where they begin to really take form. And as you seen when baking cookies, temperatures need to be near-ideal to build a proper rim. The master rim builders will even notice half a degree of ambient temperature difference and change temperatures accordingly to make sure that there is a sweet spot in temperature and humidity - 36 percent humidity at 68 degrees Fahrenheit. After molding, rims go to a different room for sanding duties as done by robots. These robots are overseen by some of ENVE’s best employees. While there is a lot of work here done by hand, a sanding machine means they can be even more consistent in their pressure. They get taken through QC after, where any final sanding and examination occurs before they get checked into inventory to be laced up and made into wheels.
Building wheels takes time and consistent precision which ENVE had down to a tee. Rims are laced up and then tensioned by machines. Every wheel is then brought to a final tension and checked over by hand, as well as a wheel truing and prestressing. It leads to a consistent, precise building profile that leads to some of the best wheels on the planet.
Completed rims are placed through this storage facility that has storage for 10,000 rims. Every one of these ENVE rims are spoken for, believe it or not. I wouldn’t be surprised if some of those are going to us, as we’ve made to work hard to have as much ENVE stock as we could. Their stuff is that good.


Of course, ENVE does a whole lot more than just rims and wheels at this point. One of their more recent additions is the ENVE SES tire. Testing is pretty darn stringent with the SES tire, as they wanted something that was among the best in class in rolling resistance, aerodynamics, and durability. There’s also an array of testing done for frames, rims, hubs, handlebars, and more.
To be clear, this isn’t everything going on at ENVE’s facility. We hope you enjoyed the highlights, that show off the truly impressive bit of capability and precision with which ENVE works. Stay tuned for our walkthrough on how the new ENVE Road custom frame is made, because that is especially impressive.
Of course, that same passion extends past the the production floor. ENVE is a company of cyclists building by cyclists, and their weekend consisting of the ENVE Builder's Round-Up and ENVE Grodeo prove just that. Be sure to check out our coverage of the ride and show if you haven't already.
Have any questions about ENVE Composites, or want to secure a handlebar, stem, or more? Give us a call during business hours or send us an email any time to info@contenderbicycles.com.

Christopher,
no problem. Thanks for checking out our tour!
Alvin - Contender Bicycles on
Thanks.
Christopher Wisniewski on